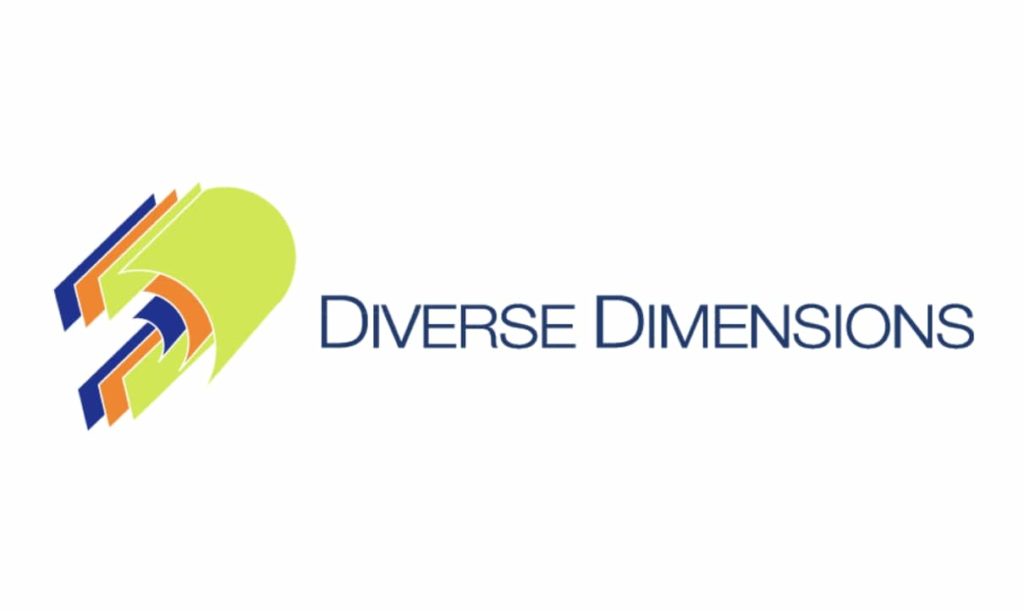
Surface/Nurbs Modeling
Surface modeling allows for rapid, accurate, as-built CAD model creation from scan data. This data is commonly used in reverse engineering and prototyping applications in a wide variety of industries. With surface modeling, imperfections inherent to each part are preserved and modeled resulting in an exact replica of a current product to then be used for downstream operations.
What is Surface/Nurbs Modeling?
Surface modeling is the creation of a CAD from point cloud or mesh data, often collected by a laser scanner. The most common file format used in the beginning of the modeling process is an STL also known as a polygonal mesh. The mesh contains many small triangles which are relatively uniform in size. The modeling process will take triangles with similar orientations and combine them to create large surface patches. The patches get stitched together and converted to CAD surfaces and exported in a universal file format (STEP or IGS).
The modeling process involves many steps but generally proceeds through hole fixing, mesh simplification, repair and refinement, and eventually modeling. There are many softwares that will model from scan data but we use GeoMagic Wrap as it offers the most flexibility and has a straight-forward workflow.
Benefits of Surface/Nurbs Modeling
Some of the biggest advantages of surface modeling include:
Preservation of As-Built Conditions
In contrast to parametric modeling, with nurbs modeling, every feature is modeled as it actually is. This is particularly useful when a custom part has been made or when you want to make an exact replica of an existing part.
Accuracy
The modeling process produces very little data loss. Certain features such as sharp edges will be rounded in both the scanning step and slightly more so when modeling, however, they can be made sharp again when the model is used as a roadmap to redraw the part in CAD. This is important to note on features that are assumed to be flat such as planes considering any form present in the part will be modeled. It is also very valuable when capturing features that are in relationship to one another such as a hole pattern.
Increased Speed to Production
Traditional methods of reverse engineering such as caliper micrometer measurements are good for prismatic parts, however, organic surfaces are much more difficult to replicate using straight-line tools. By using this method, you can quickly and accurately capture exactly what is present and begin designing around it or making modifications.
Universal file format. The files produced are universally accepted by all CAD suites so there are no formatting hurdles to overcome.
Drawbacks of Surface/Nurbs Modeling
With all its pluses, surface modeling does have some weaknesses:
Not Parametric
With a nurbs model, what you see is what you get and the model is not dynamic. For instance, there is no feature tree to change multiple features and you cannot make free-form changes to the model. That being said, holes and surfaces can be created from the model by creating new features that match the nurbs model. This is a lengthy process but a designer is still further ahead over attempting to start from scratch with hand-tools
Non-Uniform Feature Size
Every non-conformity will be captured in the model including variations in size and relationship to other features. When creating a parametric model from a Nurbs model, one will have to make some assumptions about design intent when redrawing. An example of this would be a hole size measuring 4.968 mm could be assumed to have been intended to be 5.00 mm and should be placed in the parametric model as such.
Not Always Suitable for Machining
A CNC prefers to have uniform surfaces rather than surface patches before beginning operations. Additionally, since any form in the original part will be modeled, you will want to make uniform features or risk producing an imperfect part. We have seen people cut to our nurbs models with success but it depends on the machine and the application.
When and Why Do We Use Nurbs Modeling?
A nurbs model is a great starting point for further design work. When designing around an unchangeable component or replicating an existing part or product, a nurbs model will give you an exact replica of the surfaces you’ll be working with.
You can also use nurbs modeling when seeking to improve a current product but lack a current CAD model. Creating a nurbs model in this instance will speed up the redesign process and document any changes made to the original model for future reference.
Diverse Dimensions Surface Modeling Capabilities
We have many tools at our disposal to help you on your way to nurbs model creation. From capturing the data using laser scanning or CT scanning, we can quickly and accurately create a digital version of any part or assembly.
Contact us today with any questions on surface modeling and how we may be able to use it to help solve your measurement issues.